Infrared Case Studies: Adhesive Drying
Electric Infrared Drying of Water-Based Adhesives on Envelopes
A key operation in the highly automated process of envelope production is the drying of the water-based adhesive strip on the flap for sealing the envelope. This
is normally achieved by a number of 5.5kW hot air blowers.
A critical examination of the process established the disadavantages of the existing drying method:
• | Very energy intensive. |
• | A limiting factor in setting the machine operating speed (bottleneck). |
• | Inconsistent drying. |
• | Hot and dusty working environment. |
Consequently, 22kW of hot air blowers were replaced by a 9kW thyristor controlled infrared heater enclosure. Because of the high drying efficiency of infrared,
the heater enclosure operates at only 3.5kW giving an immediate 84% reduction in energy consumption over the original drying.
The controller includes an interlock, which cuts the power to the heaters the instant the conveyor is stopped for any reason. This, coupled with the low thermal
mass of the emitter, has eliminated the need for the complex pneumatic retraction system associated with the previous drying system.
The efficient transfer of infrared energy between heat source and product removed the previous bottleneck and allowed machine speed to be increased by as much as 50%.
Because of the controllability, reliability and rapid response of the infrared system, consistent drying has been achieved
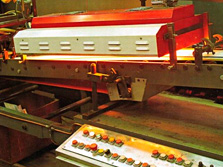
9kW Thyristor controlled infrared heater enclosure
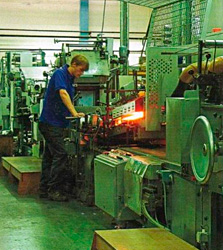
9kW Thyristor controlled infrared heater enclosure