Infrared Case Studies: Plastic and Rubber Industry Process Improvements
Electric Infrared Pre-Heating of Extruded Rubber Profiles
The 'stinger' or 'hotbox' is a traditional piece of equipment used for the pre-heating of various rubber extrusions prior to entering a longer soak
tunnel oven to fully cure the rubber. This pre-heating stage is there to kick start the curing of the rubber extrusion, to initially skin and give the rubber some
form of structural strength which is required before being supported on a conveyor belt into the final curing/soak oven.
The 'stinger' or 'hotbox' usually contains a helical formed long wave metal-sheathed element, which is made to operate at an elevated temperature of
850ºC (orange glow from element). Long wave metal-sheathed elements should operate at temperatures up to 650ºC (black to cherry red in colour). Because these
elements are made to run over temperature their life is short due to the termination points burning out. Also, after excessive use the metal structure can overheat
and inner reflectors can buckle.
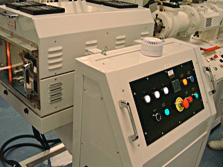
Stinger / Hotbox
- Very long warm up time.
- High running costs.
- High maintenance costs.
- Labour intensive.
- High capital cost.
- The new 'NDA Hotbox' contains medium wave emitters (or short wave depending on the application), which normally operate at 950ºC and at a higher power density than a long wave system, which produces more even heating and faster line speeds.
- The thermal response time (switch on/off) of the NDA medium wave emitters is 3 to 4 seconds and is therefore more temperature controllable.
- The 'NDA Hotbox' can achieve full warm-up time in a few minutes as opposed to 20 to 30 minutes with a long wave system.
- Internal cooling fans are used to keep the elements electrical termination points, reflectors and metalwork cool resulting in longer lamp and equipment life.
- The above 'NDA Hotbox' includes automatic temperature control, pneumatic height adjustment and safety line stop/emergency stop facility.
- Smaller high-powered short wave heater enclosures referred to, as 'muffle heaters' are available for curing rubber extruded onto the outer cores of cables and print drying on cables.
Electric Infrared Curing of a Rubber Coating
In many cases, the curing of a rubber coating applied to a textile or other substance is carried out by using either long wave infrared in the form of
metal-sheathed elements (cooker elements) or by passing the rubber coated substrate around a heated drum (rotacure).
The metal-sheathed elements are normally operated above their normal rated temperature and therefore are subject to premature failure due to the electrical
termination points burning out. The thermal response time (warm up / cool down time) of these elements is minutes, therefore requiring it to be mechanically
retracted during line stoppage. The line speeds are sloe usually very slow.
The above photograph shows a Double R Controls Ltd. fast response medium wave infrared system for the curing of rubber coating applied to a textile. The
photograph shows the three heating and extraction zones. The first zone is intended to raise the temperature of the liquid rubber coating to 100ºC, to remove any
water present. The second zone raises the coating temperature above 180ºC to remove any volatiles. The third and final zone raises the coating temperature above
280ºC to cure the rubber coating.
Benefits of Fast Response Medium Wave over Long Wave are:
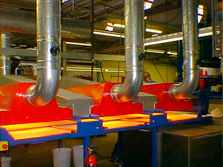
Infrared Curing
- Increased line speeds.
- Profile the heating to match the various web widths.
- 3 to 4 seconds to switch on/off, eliminating the need for a mechanical retraction system.
- The heater enclosures are air-cooled preventing over-heating of the emitters electrical terminations, extending the life of the emitter to years rather than a few months.
- Can be added to an existing process to increase throughput.
Electric Infrared Heating of Multi-Layer Plastic Laminated Products
An innovative way to produce car headliners is to use electric infrared for the heating of the multi-layered plastic laminates prior to it entering a press. The
normal method of heating the plastic laminate was by a two-station platen heater, which had the following disadvantages:
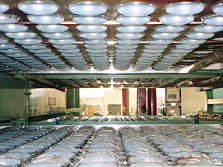
Infrared Heating System
- Very long warm up time.
- High running costs.
- High maintenance costs.
- Labour intensive.
- High capital cost.
- Double shot process (1 shot to mould, 1 shot to cloth laminate).
The platen heaters were replaced with a short wave infrared blown bulb system designed to heat the plastic laminate from both above and below. The infrared
heating system was split into two heating zones, each of which was temperature controlled by means of non-contact temperature pyrometers.
The infrared heating system was designed to mould and cloth laminate simultaneously. The advantages of using electric infrared are:
- The short wave blown bulb switches on to full power within 2 seconds, therefore the heating process can start virtually immediately after switch on.
- One-shot heating and laminating process.
- Faster heating process.
- Increases in throughput.
- Less labour intensive.
- Infrared is a low cost alternative heating technique.