Infrared Case Studies: Textiles and Fabrics
Contents
Electric Infrared Pre-Heating on a Stenter Dryer
Stenter dryers are the workhorses of the web textile finishing industry for drying and heat setting of many different types of fabrics. They consist of several
large hot-air recirculation chambers known as bays through which the fabric is transported in a single pass stretched between pin-chain or clip-chain continuous
conveyors. The air can be heated by steam, oil, gas or electricity.
In this type of dryer, a significant portion (typically 30%) of the infeed is devoted to heating up (sensible heat) the fabric and any water load. By adding a
metre or two of electric infrared (medium wave, approx 30kW/m²) at the front entry of the Stenter as a pre-heater, the working temperature or point at which
evaporation (latent heat) takes place occurs much earlier and therefore the Stenter speed can be increased.
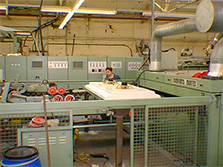
Pre-heating on a Stenter dryer
- The use of infrared for pre-heating is a low cost alternative to adding an additional bay to a Stenter dryer to increase throughput.
- Infrared requires less space than an additional Stenter drying bay.
- The Infrared pre-heater enclosure can generally be retrofitted over the width adjustable conveyor by means of a simple support framework.
- Increases in line speed of 10% to 30% can be achieved depending on present line speed, weight of cloth, moisture contents and infrared kW installed.
- Free of charge on-site trials can be carried out by one of our engineers.
Electric Infrared Post-Curing of Coatings
Cross-linking or curing of most coatings applied to a textile is normally carried out at higher temperatures (160ºC to 180ºC) than for drying (120ºC to 160ºC).
Some dryers because of their age or design, cannot reach these higher cross-linking/curing temperatures and, therefore, have to be passed through a second heating
process to achieve curing. The additional handling and energy to run the second process is not a cost effective solution.
We know the fabric and the coating will be dry at a temperature of between 120ºC to 160ºC. By adding a module of electric infrared immediately at the output end
of the oven, we are able to quickly elevate the temperature of the fabric/coating to the necessary cross-linking/curing temperature (160ºC to 180ºC). It is
important not to have any large gaps between the out feed of the oven and the in feed of the infrared module thus preventing any temperature in the fabric to be lost.
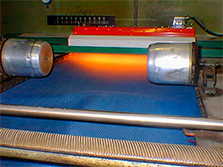
Post-Curing
- The use of infrared for post-curing of coatings on an existing dryer removes the need for additional handling and saves on the energy required to run a second line and, in some circumstances, a much slower heating process.
- By post-curing with infrared, bottlenecks in production can be removed.
- Increases in line speed can be achieved by post-curing with infrared.
- The infrared modules can be retrofitted on to an existing dryer, therefore not taking up precious space.
- Infrared is a low cost alternative heating technique.
- Free of charge on-site trials can be carried out by one of our engineers.
Electric Infrared Heating/Curing of Coatings Prior To Embossing
In many cases, the heating/curing of a coating applied to a textile prior to say an embossing process is carried out by using long wave infrared in the form of
metal sheathed elements (cooker elements). These particular elements are normally operated above their normal rated temperature and, therefore, are subject to
premature failure due to electrical termination points burning out. The thermal response time (warm up/cool down) of these elements is several minutes, therefore,
requiring the elements be mechanically retracted during a line stoppage. The line speeds are also usually very slow.
In this type of dryer, a significant portion (typically 30%) of the infeed is devoted to heating up (sensible heat) the fabric and any water load. By adding a
metre or two of electric infrared (medium wave, approx 30kW/m²) at the front entry of the Stenter as a pre-heater, the working temperature or point at which
evaporation (latent heat) takes place occurs much earlier and therefore the Stenter speed can be increased.
The above photograph shows a Double R Controls Ltd. Fast Response Medium Wave infrared System for the curing of an oil based coating applied to a textile
prior (on some products) to an embossing process. The benefits of the aboves system to a long wave system are:
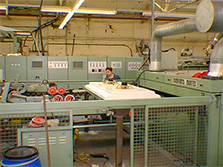
Pre-heating on a Stenter Dryer
- The use of infrared for pre-heating is a low cost alternative to adding an additional bay to a Senter dryer to increase throughput.
- Infrared requires less space than an additional Stenter drying bay.
- The infrared pre-heater enclosure can generally be retrofitted over the width adjustable conveyor by means of a simple support framework.
- Increases in line speed of 10% to 30% can be achieved depending on present line speed, weight of cloth, moisture contents and infrared kW installed.
- Free of charge on-site trials can be carried out by one of our engineers.